Down hole Completion Equipment
Horizon Trading Development is an engineering consulting company in field of improving and developing the quality and cost effective of product and services in oil and gas industry. Recruiting skilled and proficient engineers that have been worked in various well completion industries for years, this company has been acquired the technology of and domestic design production of down hole completion equipment for oil and gas wells.
HTD Co. provides for customers comprehensive range of fully integrated “Completion Systems,” which package and integrate equipment, products, processes, procedures and programs to provide a combination of best-in-class and fit-for-purpose products and services. HTD co. has been recruited specialists in design, quality control, project control and planning and is ready to supply complete down hole completion equipment in highest quality.
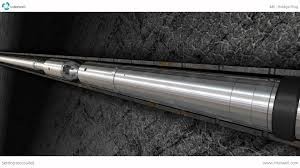
In order to provide Localized and fit-for-purpose production that meets customer needs, HTD’s design team is qualified to redesign available productions to acquire specific technical requirements in functioning, strength and corrosion resistance performance, as well as to preserve the consistency and interoperability with other original types.
Safety Valve Landing Nipple
The HTD’s Wireline Retrievable Safety Valve is a self-equalizing, flapper-type, surface-controlled, subsurface, wireline safety valve. The wireline valve incorporates a modular concept to allow flexibility and adaptability to existing and new completions. HTD safety valves may be supplied with a HTD lock mandrels, or as a subassembly with adapter to a standard lock. When safety valves are assembled to a safety valve lock, the model designation is expanded to include the lock and the safety valve nipple into which it is landed. The Safety Valve Lock must be compatible with the Nipple Profile.
When properly installed, the valve is hydraulically controlled from the surface via a stainless steel control line that connects the Landing Nipple to the surface Emergency Shutdown System. Loss of control line pressure will close the valve and shut-in the well.
Features
- Equalizing-type flapper closure.
- Equalizing system, Sealing and seating surfaces are out of the flow path of well production when valve is in the open position.
- Strong and reliable closure system
- Solid construction flapper made from high strength and corrosion resistant material
- Spherical radius seat on flapper improves metal-to-metal seal reliability
- Low pressure sealing is acquired in closed position by Resilient seal system
- Equalizing system ensures easy opening process
- Low-friction sealing system facilitates both opening and closing cycles
- Manufactured from Highly resistant material this product is fully fitted for sour service
- High pressure – high temperature service is available by reliable packing system
Benefits
- Minimal hinge pin stress during opening and closing cycle.
- Metal-to-metal sealing for increased reliability.
Tubing Size | Seal Bore Size (in) | Drift Size (in) | Max. Setting Depth (ft) | Opening Pressure (psi) | Pressure Rating (psi) | Temperature Rating (C) |
---|---|---|---|---|---|---|
5” | 3.812 | 2.126 | 1000 | 1200 + shut-in pressure | 6000 | 20 - 200 |
7” | 5.950 | 3.267 | 1000 | 6000 | 20 - 200 | |
7” | 5.963 | 1000 | 6000 | 20 - 200 |
Safety Valve Landing Nipple
Safety valve landing nipples are installed integral to the tubing string and provide a means of locating and locking a wireline retrievable safety valve in place. The wireline retrievable safety valve (WRSV) is locked in place by using the locking profile integral to the landing nipple.
The safety valve landing nipples are ported for control line fluid communication from the surface to operate a down-hole safety valve. The landing nipples are also designed to withstand loads from the tubing string to ensure long-term reliability of the safety valve system.
Features
- Maximum ID is compatible with tubing size and weight.
- Control port machined into nipple wall.
- Robust control line connection – metal-to-metal jam nut ensures reliable sealing
- Eccentric control line lug – machined control line inlet protects the control line while installing
- Large bore design – allows access to lower completion by offering a full bore ID
Benefits
- Wire-line operator controls locating, landing and locking safety valve in a preselected location.
- Locking principle is designed to hold against pressure from either direction and sudden and/or repeated reversals of pressure
- Rugged, non-welded design.
Tubing Size | Seal Bore Size (in) | Max. OD | Pressure Rating (psi) | Port Size (in) |
---|---|---|---|---|
5” | 3.812 | 5.787 | 7000 | 0.250 |
7” | 5.950 | 8.267 | 5000 | 0.250 |
7” | 5.963 | 0.250 |
Expansion Joint
The Expansion Joints are designed to be used in single and dual – string completion to accommodate changes in tubing length caused by variations in pressure, temperature or both. They are capable of maintaining the pressure integrity of tubing while allowing the string to safely expand and contract. The Expansion Joint can be run above Packers. The proper placement and stroke selection of these splined slip joints reduce the chances of over stressing the well tubing during production, acidizing, fracturing and other well operations. Alloy-steel construction gives these joints high body and end-connection tensile strength. Stroke length may be changed in the field. The splines transmit torque through the joint.
The travel joint consists of a top sub, outer mandrel, inner mandrel and shear sleeve. The packing stack is retained by the retainer cap. An o-ring is installed in the top sub. Sheer pins hold the travel joint in the fully ex tended, closed or partially open condition and at one foot interval. The travel length of the joints can be 10ft or 20ft.
Features
- Allow tubing torque below by engagement of slots.
- Available in standard tubing sizes.
- Maintains pressure integrity during expansion and contraction
- Adjustable shearing value
- Adjustable pinned length at intervals of 1 ft.
Benefits
- Stroke length is as required.
- Available in versions that may be locked in open, mid-stroke, or closed positions
Tubing Size | Maximum OD (in) | Pressure Rating(psi) | Temperature Rating(C) |
---|---|---|---|
41/2” | 5.740 | 5000 | 20 - 150 |
51/2” | 7.690 | 5000 | 20 - 150 |
41/2” | 5.740 | 10,000 | 20 - 150 |
51/2” | 7.690 | 10,000 | 20 - 150 |
Side Pocket Mandrel (SPM)
The side pocket mandrel is made up as an integral part of the production tubing when preparing a well for gas lift, chemical injection, water flood or other special applications. This mandrel is designed to be installed in straight hole wells. HTD’s side pocket mandrels are designed with a round cross-section body and are available in a variety of tubing threads and sizes for installation as part of the tubing string. Standard non-orienting kick over tools are utilized in this mandrel to install and retrieve flow control devices by standard wireline methods
The side pocket mandrel’s tubular pocket consists of a locking recess located below a top no-go and two polished bores straddling ports which provide communication between the casing annulus and the tubing. The wireline flow control devices have packing which seal in the polished bores above and below the ports in the mandrel pocket.
Features
- An orienting sleeve.
- An integral discriminator and pocket.
- Each side pocket mandrel is inspected and tested under the guidelines of a Quality Assurance Program which includes wet magnetic particle inspection, hardness value test, hydrostatic pressure test and ID/OD drift.
- All mandrels are made from fully traceable material.
- Compatible with other manufacturers’ flow control devices.
Benefits
- Precise alignment and insertion of side pocket devices into the mandrel side pocket.
- Large tools deflected into the tubing bore.
Tubing Size | Max. OD (in) | Pocket Size (in) | Pressure Rating |
---|---|---|---|
41/2” | 5.984 | 1.000 | 5000 |
51/2” | 7.755 | 1.500 | 5000 |
41/2” | 5.984 | 1.000 | 10,000 |
51/2” | 7.755 | 1.500 | 10,000 |
Sliding Side Door (SSD)
Sliding Side Door (SSD) is a down hole equipment that allows communication between the tubing and annulus for circulation or selective-zone production. The HTD’s SSD is high performance, Non-elastomeric equalizing sliding sleeve. When desired, the sleeve can be shifted open or closed using standard wireline methods and equipment. The tool is designed such that any lock profile and compatible seal bores can be specified and ordered to accept a wide range of Wireline Locks, and accessories. The sleeve is available in downshift-to-open or upshift-to-open versions.
Features
- Nipple profiles are available on request.
- Polished pack-off area.
- Packing dose not move when the sleeve is shifted.
- A specially designed Diffuser Ring made of high-strength thermoplastic is critically spaced between the flow ports and the upper packing unit.
- The seal stack is manufactured from high-strength, non-elastomeric compounds.
- Mill slots replace drill holes as flow ports on both the housing and the insert to allow more flow area, reduce erosion and allow higher torque and tensile strengths through the sleeve.
- Locating the threaded connection inside the primary seal stack eliminates the need for O-ring thread seals and cuts the number of potential leak paths in half.
Benefits
- Reliable shifting for the life of the well.
- Sleeve can be shifted even when outside of sleeve is packed with stand.
- Instance equipment can be shifted on a single trip of the slick-line.
- Inner sleeve can be shifted repeatability.
Tubing Size | Max. OD.(in) | Profile Size (in) | Pressure Rating (psi) | Temperature Rating (C) |
---|---|---|---|---|
41/2 “ | 5.500 | 3.688 | 6000 | 20-200 |
51/2” | 6.500 | 4.562 | 6000 | 20-200 |
41/2 “ | 5.500 | 3.688 | 10,000 | 20-200 |
51/2” | 6.500 | 4.562 | 10,000 | 20-200 |
Anchor Seal / Ratch Latch
The anchor tubing seal assembly is used as an alternative to set-down weight; it prevents seal movement or is used when it is preferable to land the tubing in tension. The anchor tubing seal assembly is run in on the production string. Set-down weight causes the anchor’s threaded latch to engage the corresponding threads in the top of the packer. Once engaged, the anchor and tubing are securely locked in place. Any tubing contraction will cause a tensile load to be applied to the tubing string. Care must be taken to ensure tensile forces that develop will not part the tubing whenever an anchor is used. To release the anchor, it must be rotated to the right 10 to 12 turns at the packer.
Features
- A solid nut anchor with special 2 TPI left hand square thread creates a metal to metal seal with the packer when sufficient set down is applied.
- High Quality Seals has been adopted for high pressure / high temperature conditions
- Premium thread has been utilized instead of O-ring in extension
Casing Size | Casing Weight (lb/ft) | Maximum OD (in) | Pressure Rating (psi) |
---|---|---|---|
7” | 29 | 5.000 | 5000 |
95/8” | 36-47 | 6.910 | 5000 |
7” | 29 | 5.000 | 10,000 |
95/8” | 36-47 | 6.910 | 10,000 |
Permanent Packer
The HTD packer is a hydraulically set permanent packer that features the largest possible bore through combined packer and seal accessory. This Packer is run to depth, connected to the tubing with a compatible Anchor Seal and set by applied tubing pressure. This makes the packer ideal for use in high angle deviated wells.
The packer comprises an upper seal bore with a left hand square thread, a high pressure/high temperature Alfas packing element system, straddled by upper and lower slip rings, and a setting piston. A solid nut anchor with nose seal provides a metal to metal seal between the production tubing and the packer when sufficient set down load is applied. A chevron seal stack backs this seal up and operates when insufficient set down load is applied to effect a metal to metal seal.
Features
- One piece mandrel and seal-bore.
- Case carburized slips.
- Metal-to-metal backup shoes with 360° casing wall contact.
- Ratch-Latch seal-bore with seal anchor.
- The packing element is resistant to swabbing which enhances reliability and allows increased running speed.
- Two opposed sets of full circle slips allow the load to be distributed evenly around the casing wall and ensure the packer remains where it was set.
- Interlocked expandable metal back-up rings contact the casing and create a positive barrier to packing element extrusion.
- The packing element system consists of a single piece packing element design that is self-energized from the initial set condition.
Benefits
- Potential leak paths minimized.
- No tubing manipulation required during string.
- Greater running clearance because of low profile of external components.
Casing Size | Casing Weight (lb/ft) | Maximum OD (in) | Seal Bore (in) | Pressure Rating (psi) |
---|---|---|---|---|
7” | 29 | 5.875 | 4.750 | 5000 |
95/8” | 36-47 | 8.125 | 6.500 | 5000 |
7” | 29 | 5.875 | 4.750 | 10,000 |
95/8” | 36-47 | 8.125 | 6.500 | 10,000 |